Corrosion inhibitor testing and chemical selection are among our specialist capabilities and our extensive experience positions us as your ideal service provider.
Performing corrosion inhibitor testing and optimising chemical selection are critical aspects of maximising the lifespan and safeguarding the integrity of oil and gas infrastructure.
In the oil and gas industry, carbon steel remains the first-choice material for the construction of new pipelines. However, as operating conditions become increasingly extreme, materials are being pushed to their limits.
Along with ageing assets and equipment operating beyond its projected lifespan, these factors contribute to a heightened risk of materials failure.
Failure mechanisms that impact carbon steel pipelines are typically localised events such as pitting, weld corrosion or flow-assisted corrosion. As production conditions can contribute to the severity of these processes, operating environments also need to be considered during the design of any testing programme.
Intertek CAPCIS has a long story and extensive experience in investigating specific issues such as inhibition in wet gas pipelines, test procedure development and mechanisms of inhibition. Choosing a partner with specialist facilities and experience will ensure that you receive accurate and reliable guidance on the optimal use of materials and chemicals.
Our test programmes are developed following a detailed review of operating conditions and addressing the specific needs of the client to define key performance parameters. Where necessary, bespoke test rigs and procedures can be designed to simulate specific problems.
Intertek CAPCIS has developed specialised tests to assess inhibition of specific issues relating to Oil & Gas production, including:
- Preferential weld corrosion
- Pitting corrosion in sour service
- Top-of-line corrosion simulation and evaluation of batch treatment
- Under-deposit corrosion
- High wall shear stress simulation
- Erosion corrosion
Our global network of experts have a deep knowledge of CO2 corrosion, H2S corrosion and galvanic corrosion is key to successfully mitigating general corrosion, as well as preferential weld, localised and top-of-the-line corrosion.
Utilising the facilities and apparatus in our dedicated laboratories - flow loops, high-pressure dynamic autoclaves and advanced electrochemical monitoring systems - even extreme well conditions can be simulated including brine chemistries, flow regimes, a range of temperatures and acid gas partial pressures.
Moving beyond corrosion inhibitor testing and chemical selection, we can support your business with a full Total Quality Assurance suite of related exploration and production services.
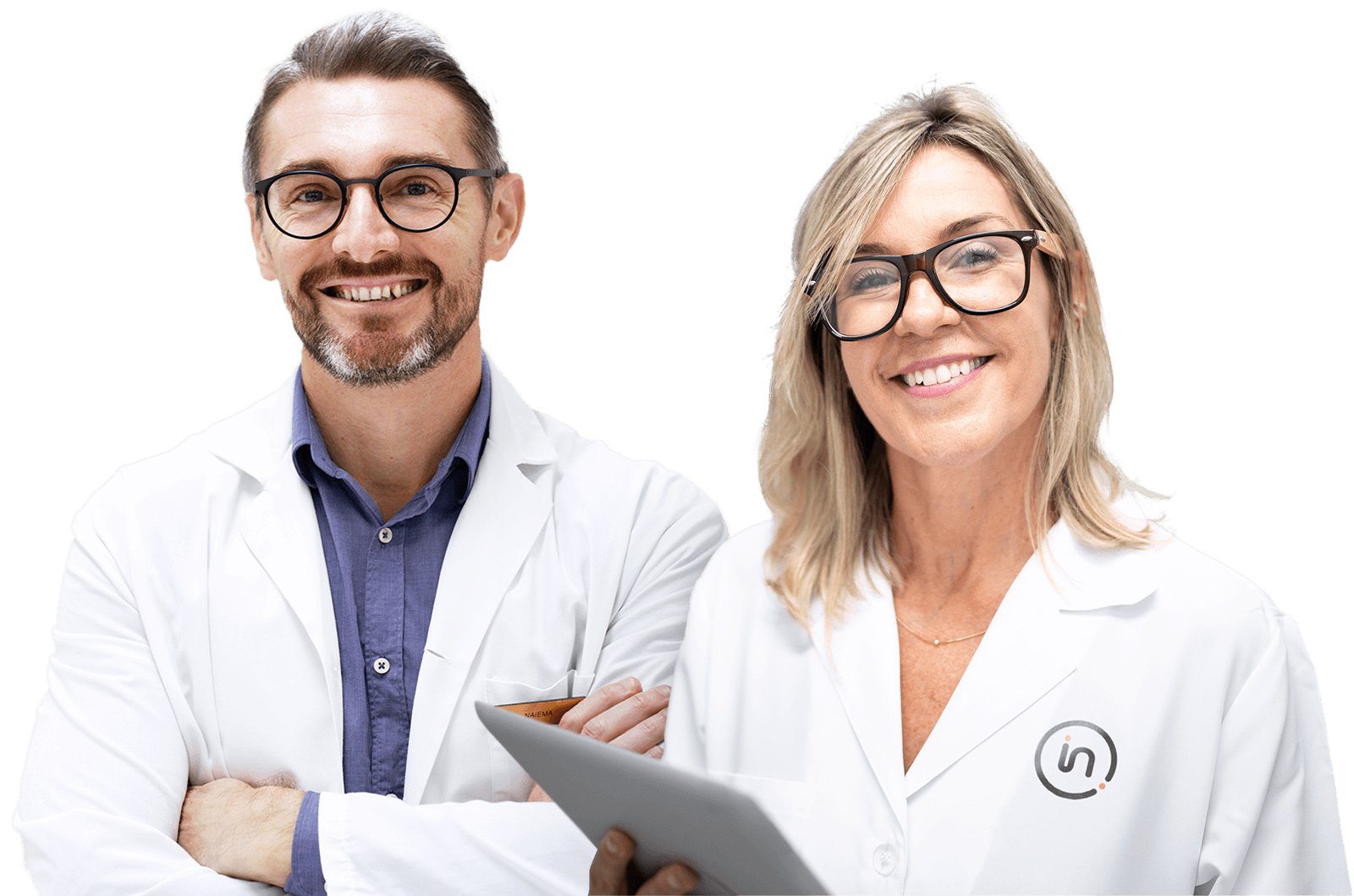